Az elülső és a hátsó felület közötti szög. Vágóelemek és geometria
A φ vezetőszög határozza meg a vágás szélessége és vastagsága közötti összefüggést az előtolás és a fogásmélység állandó értékei mellett. A φ főszög csökkenésével a vágás vastagsága csökken, szélessége pedig nő. Ez az él aktív hosszának, azaz a munkadarabbal érintkező hosszának növekedéséhez vezet. Csökken a vágási erő és a hőmérséklet egységnyi élhosszon, és ezzel egyidejűleg csökken a maró kopása is. A φ szög csökkenésével az Ru forgácsolóerő sugárirányú komponense meredeken növekszik, ami a munkadarab elhajlásához vezethet, és elégtelen rögzítés esetén akár ki is szakíthatja a középpontokból. Ugyanakkor működés közben rezgések jelenhetnek meg.
A kísérleti munka azt mutatja, hogy a φ szög csökkenésével állandó előtolás mellett a szerszám élettartama meredeken növekszik, míg állandó vágási vastagságnál a szerszám élettartama a φ szög változásától függetlenül szinte állandó marad. Ebből következik, hogy a maró tartósságát főként a vágás vastagsága befolyásolja - megközelítőleg megegyezik a φ szöggel. A vágásvastagság növekedésével a tartósságra gyakorolt befolyása növekszik. Ezért a termelékenység növelése érdekében kis φ szögek alkalmazása javasolt állandó vágási vastagság mellett, a vágóél szilárdságához viszonyítva maximálisan megengedett, és ennek megfelelő (lehetséges) előtolás-növekedéssel az s = a/ képlet szerint. sin φ A vágási mód ilyen megválasztása csak merevség és rezgésálló AIDS rendszer mellett és kis feldolgozási ráhagyással lehetséges. Javasolt a φ síkszögek használata (fokban):
Nehéz körülmények között végzett kikészítéshez... 10-20
Nehéz körülmények közötti feldolgozásnál, ha l/d<6 ... 30-45
Enyhe munkakörülmények között l/d=6-12 ... 60-75
Kis átmérőjű l/d>12 ... 90 hosszú munkadarabok megmunkálásakor
Rizs. 7 - Főszög φ
Így például a nagy és masszív alkatrészek megmunkálásakor nagy merevségű gépeken a legnagyobb tartósság szempontjából előnyös 10-20°-os befutási szögű marókat használni. Ellenkezőleg, a nem merev alkatrészek, például görgők, perselyek, anyacsavarok, fúrók, dörzsárak stb. megmunkálásakor nagy φ = 60-75°-os szögekkel javasolt dolgozni. Ha ezeknek az alkatrészeknek vállak és lépcsők vannak, akkor célszerű φ = 90°-os marókat használni. Lehetővé teszik az átvágásos megmunkálás mellett a keresztirányú esztergálást is, így nincs szükség a maró cseréjére. Az olyan alkatrészek esetében, mint a lépcsős görgők, ez a feldolgozás jelentős időmegtakarítást eredményez a marók átrendezésével kapcsolatban. A szerszámgépiparban jelentős számú ilyen alkatrész található; Emiatt a szerszámgépgyártók gyakran használnak φ - 90°-os marókat.
Főre
harmadik szakasz
A fémforgácsolás elméletének alapjai.
Vágási módok kiválasztása
fejezet VI
A fémforgácsolás elméletének alapjai
A fémvágás elméletének megalapítói kiváló orosz tudósok voltak, I. A. Time (1838-1920), K. A. Zvorykin (1861-1928), G. Usachev (1873-1941) stb. E tudósok munkái világszerte elismertek. még nem veszítették el értéküket. Az elmaradott cári Oroszország körülményei között azonban mindez a munka nem talált gyakorlati alkalmazásra, mivel az ipar gyengén volt fejlett.
A fémvágás tudománya csak a Nagy Októberi Szocialista Forradalom után kapott szélesebb kört, különösen a szovjet ötéves tervek idején, amikor a tudomány a szocialista ipar szolgálatába állt.
V. D. Kuznyecov, V. A. Krivoukhov, I. M. Beszprozvannij, A. M. Rosenberg, M. N. Larin, P. P. Trudov, M. I. Klushin és mások szovjet tudósok létrehozták a fémek forgácsolásának hazai iskoláját, amelynek megkülönböztető jellemzője a tudomány és a termelés szoros együttműködése, a tudósok a termelés újítóival. .
A fémforgácsolás tudományának fejlődésében nagy szerepet játszott a gyártásújítók mozgalma. A munka termelékenységének növelése érdekében a termelési vezetők új utakat kezdtek keresni a forgácsolási feltételek javítására: új forgácsolószerszám-geometriát hoztak létre, megváltoztatták a vágási feltételeket és új vágóanyagokat sajátítottak el. Egy innovatív esztergályos minden munkahelye a vágási folyamat kutatásának kis laboratóriumává vált.
A csak szocialista gazdaságban lehetséges széles körű tapasztalatcsere, valamint a vezető iparosok és a tudomány szoros együttműködése biztosította a fémforgácsolás tudományának gyors fejlődését.
1. A vágó munkája
Klin és munkája. Bármely vágószerszám működő része az ék(44. ábra). Az alkalmazott erő hatására az ék hegye belevág a fémbe.
Minél élesebb az ék, vagyis minél kisebb az oldalai által bezárt szög, annál kisebb erő szükséges a fémbe vágásához. Az ék oldalai által alkotott szöget ún pontszögés a görög β betűvel jelöljük ( béta). Következésképpen minél kisebb a β kúposszög, annál könnyebben hatol be az ék a fémbe, és fordítva, minél nagyobb a β kúposszög, annál nagyobb erőt kell kifejteni a fém vágásához. Az élezési szög hozzárendelésénél figyelembe kell venni a feldolgozandó fém mechanikai tulajdonságait. Ha a kemény fémet kis β élezési szögű maróval vágja, akkor a vékony penge nem tartja magát, és összeomlik vagy eltörik. Ezért a megmunkálandó fém keménységétől függően az ék megfelelő élezési szöge van hozzárendelve.
A közvetlenül a vágó előtt elhelyezkedő megmunkálás alatt álló fémréteget az elülső felülete folyamatosan összenyomja. Amikor a vágó ereje meghaladja a fémrészecskék tapadási erejét, az összenyomott elem leszakad, és az ék elülső felületével felfelé mozog. A kifejtett erő hatására előrehaladó vágó továbbra is összenyomja, forgácsolja és eltolja azokat az egyes elemeket, amelyekből a forgács keletkezik.
Alapmozgások forduláskor. Esztergagépen történő feldolgozáskor a munkadarab forog, és a vágó hossz- vagy keresztirányú mozgást kap. A munkadarab forgását ún fő mozgás, és a vágó mozgása az alkatrészhez képest az etető mozgás(45. ábra).

2. Esztergaszerszám főbb részei, elemei
A vágó két fő részből áll: a fejből és a testből (rúdból) (46. ábra). Fej a vágó munka (vágó) része; test a vágó rögzítésére szolgál a szerszámtartóban.

A fej a következő elemekből áll: elülső felület, amely mentén a forgácsok folynak, és hátsó felületek, a munkadarab felé néz. A vágási felület felé néző egyik hátsó felület ún fő-; a másik a kezelt felület felé néz - kiegészítő.
A vágóélek az elülső és a hátsó felületek metszéspontjából származnak. Megkülönböztetni itthonÉs segédvágóélek. A fő vágóélt a fő vágóél végzi.
A fő- és segédvágóél metszéspontját ún a metszőfog hegye.
3. Felületkezelés
A munkadarabon háromféle felület található (47. ábra): megmunkált, megmunkált és vágófelület.

Feldolgozott A felület a munkadarab azon felülete, amelyről a forgácsot eltávolítják.
Kezelt felület a forgács eltávolítása után kapott alkatrész felülete.
Vágási felület a munkadarabon a maró fő vágóéle által kialakított felület.
Különbséget kell tenni a vágósík és a fősík között is.
Vágó sík a vágófelületet érintő és a maró vágóélén áthaladó síknak nevezzük.
Fő sík a vágó hossz- és keresztirányú előtolásával párhuzamos síknak nevezzük. Esztergagépeken egybeesik a szerszámtartó vízszintes tartófelületével.
4. Vágószögek és rendeltetésük
A vágó munkarészének szögei nagymértékben befolyásolják a vágási folyamatot.
A vágó szögeinek helyes megválasztásával jelentősen megnövelheti folyamatos működésének időtartamát a tompítás előtt (tartósság), és időegységenként (percenként vagy óránként) nagyobb számú alkatrészt dolgozhat fel.
A vágószögek megválasztása meghatározza a maróra ható forgácsolóerőt, a szükséges teljesítményt, a megmunkált felület minőségét stb. Ezért minden esztergályosnak alaposan tanulmányoznia kell az egyes maró élezési szögeinek rendeltetését, és tudnia kell helyesen elvégezni. válassza ki a legelőnyösebb értéküket.
A vágószögek (48. ábra) főszögekre, vágóélszögekre és a fő vágóél dőlésszögére oszthatók.

A főbb szögek a következők: hátsó szög, elülső szög és pontszög; A tervben lévő vágási szögek tartalmazzák a fő és a segédszögeket.
A vágó fő szögeit a fő vágási síkban kell mérni, amely merőleges a vágási síkra és a fősíkra.
A vágó munkarésze egy ék (a 48. ábrán árnyékolva), amelynek alakját a maró elülső és fő hátsó felülete közötti szög jellemzi. Ezt a szöget ún pontszögés a görög β (béta) betűvel jelöljük.
Hátsó szög α ( alfa) a fő oldalfelület és a vágási sík közötti szög.
Az α hézagszög a maró oldalfelülete és a munkadarab közötti súrlódás csökkentését szolgálja. A súrlódás csökkentésével ezáltal csökkentjük a maró felmelegedését, amely emiatt kevésbé kopik. Ha azonban a hézagszöget jelentősen megnöveljük, a vágó gyengül és gyorsan összeesik.
Elülső szög γ ( gamma) a maró elülső felülete és a fő vágóélen keresztül húzott vágósíkra merőleges sík közötti szög.
A γ dőlésszög fontos szerepet játszik a forgácsképzési folyamatban. A dőlésszög növekedésével a vágó könnyebben tud belevágni a fémbe, csökken a vágott réteg deformációja, javul a forgácsáramlás, csökken a forgácsolóerő és az energiafogyasztás, valamint a megmunkált felület minősége javítva van. Másrészt a dőlésszög túlzott megnövekedése a vágóél gyengüléséhez és szilárdságának csökkenéséhez, a vágóél forgácsolódása miatti maró fokozott kopásához, valamint a hőleadás romlásához vezet. Ezért a kemény és törékeny fémek megmunkálásakor a szerszám szilárdságának és tartósságának növelése érdekében kisebb dőlésszögű marókat kell használni; Puha és szívós fémek megmunkálásakor nagy dőlésszögű marókat kell használni a forgács eltávolításának megkönnyítésére. A gyakorlatban a gereblye szögének megválasztása a megmunkálandó anyag mechanikai tulajdonságain túl a vágó anyagától és a gereblye felületének alakjától is függ. A keményfém marógépekhez javasolt dőlésszög értékeket a táblázat tartalmazza. 1.
Szögek tervezése. Fő tervszög φ ( fi) a fő vágóél és az előtolás iránya közötti szög.
A φ szöget általában 30-90° tartományban választják meg a megmunkálás típusától, a maró típusától, a munkadarab és a maró merevségétől és rögzítésük módjától függően. A legtöbb fém folyamatos nagyoló marógépekkel történő feldolgozásakor φ = 45°-os szöget vehet fel; Vékony, hosszú alkatrészek középpontban történő megmunkálásakor 60, 75 vagy akár 90°-os vezetési szögű marókat kell használni, hogy az alkatrészek ne hajoljanak vagy remegjenek.
Segédsíkszögφ 1 a másodlagos forgácsolóél és az előtolás iránya közötti szög.

Szög λ ( lambda) a fő vágóél megdöntése(49. ábra) a fő vágóél és a maró tetején a fősíkkal párhuzamosan húzott vonal közötti szög.
Asztal 1
A keményfém marógépekhez ajánlott dőlésszög és hátszög értékek
Jegyzet: A fémek mechanikai tulajdonságait speciális gépekkel és műszerekkel határozzák meg, és minden tulajdonság saját megjelölést kap. Az ebben és a következő táblázatokban megadott σ b jelölés a fém szakítószilárdságát fejezi ki; ennek a határértéknek az értéke kg/mm2. A HB betűk a fém keménységét jelzik, amelyet Brinell műszeren úgy határoznak meg, hogy egy edzett acélgolyót a fém felületébe nyomnak. A keménységi értéket kg/mm2-ben mérik.
Olyan marók, amelyeknél a csúcs a vágóél legalacsonyabb pontja, azaz λ szög pozitív(49. ábra, c) tartósabbak és ellenállóbbak; Ezek a marók alkalmasak keményfémek megmunkálására, valamint nem folytonos felületekre, amelyek ütési terhelést okoznak. Az ilyen felületek keményfém marókkal történő megmunkálásakor a fő vágóél dőlésszögét 20-30°-ra kell beállítani. Olyan marók, amelyek csúcsa a vágóél legmagasabb pontja, azaz λ szög negatív(49. ábra, a)) lágyfémekből készült alkatrészek megmunkálására ajánlott használni.
5. Vágók gyártásához használt anyagok
A maró vágóélein végzett munka során nagy nyomás, valamint magas hőmérséklet (600-800° és afölött) lép fel. A maró hátsó felületének súrlódása a vágófelületen és a forgácsok a maró elülső felületén a munkafelületek többé-kevésbé gyors kopását okozzák. A kopás következtében a vágórész alakja megváltozik, és egy idő után a vágó alkalmatlanná válik a további munkára; az ilyen vágót le kell venni a gépről és le kell földelni. Annak érdekében, hogy a maró újraköszörülés nélküli élettartamát növelje, szükséges, hogy az anyag jól ellenálljon a magas hőmérsékleten történő kopásnak. Ezenkívül a vágóanyagnak elég erősnek kell lennie ahhoz, hogy törés nélkül ellenálljon a vágás során fellépő nagy nyomásoknak. Ezért a vágóanyaggal szemben a következő alapkövetelményeket kell támasztani: keménység magas hőmérsékleten, jó kopásállóság és szilárdság.
Jelenleg számos szerszámacél és ötvözet létezik, amely megfelel ezeknek a követelményeknek. Ide tartoznak: szén szerszámacélok, gyorsacélok, keményötvözetek és kerámia anyagok.
Carbon Tool Steel. A vágószerszámok gyártásához 0,9-1,4% széntartalmú acélt használnak. Edzés és temperálás után az ebből az acélból készült vágószerszámok nagy keménységet kapnak. Ha azonban a forgácsolás során a vágóél hőmérséklete eléri a 200-250°-ot, az acél keménysége meredeken csökken.
Emiatt a szén-szerszámacél jelenleg korlátozottan használható: olyan vágószerszámokat készítenek belőle, amelyek viszonylag kis forgácsolási sebességgel működnek, amikor a vágási zóna hőmérséklete kis értéket ér el. Ilyen szerszámok a következők: matricák, dörzsárak, menetfúrók, reszelők, kaparók stb. A vágószerszámok jelenleg nem szénacélból készülnek.
Gyorsacélok. A gyorsacélok nagyszámú speciális, úgynevezett ötvözőelemet tartalmaznak - volfrámot, krómot, vanádiumot és kobaltot, amelyek az acélnak magas forgácsolási tulajdonságokat adnak - képesek megőrizni a keménységet és a kopásállóságot, amikor a vágási folyamat során 600-ra hevítik. 700°. A nagysebességű acélvágók 2-3-szor nagyobb vágási sebességet tesznek lehetővé, mint a szénvágóké.
Jelenleg a következő típusú gyorsacélokat gyártják a Szovjetunióban (GOST 9373-60): R18, R9, R9F5, R14F14, R18F2, R9K5, R9KYu, R10K5F5 és R18K5F2.
A teljes egészében gyorsacélból készült marók drágák, ezért a gyorsacél megtakarítása érdekében elsősorban hegesztett lemezes marókat használnak.
Kemény ötvözetek. A keményötvözeteket nagyon nagy keménység és jó kopásállóság jellemzi.
A karbidötvözetek lemezek formájában készülnek szénnel kombinált volfrám- és titánporokból. A szén és a volfrám kombinációját ún keményfém, és titán - titán-karbiddal. Kötőanyagként kobaltot adnak hozzájuk. Ezt a porkeveréket nagy nyomáson préselik kis lemezek előállítására, amelyeket azután körülbelül 1500 °C-on szinterezünk. A végül elkészített lemezek nem igényelnek hőkezelést. A lemezt rézzel forrasztják egy szénacél vágótartóra, vagy rögzítik hozzá állítókkal és csavarokkal (mechanikus betétrögzítés).
A keményötvözetek fő előnye, hogy jól ellenállnak a forgácsokból és a munkadarabból származó kopásnak, és 900-1000°-ra hevítve sem veszítik el vágási tulajdonságaikat. Ezeknek a tulajdonságoknak köszönhetően a keményfém lapkákkal felszerelt marók alkalmasak a legkeményebb fémek (kemény acélok, beleértve az edzetteket is) és nemfémes anyagok (üveg, porcelán, műanyagok) megmunkálására a forgácsolási sebesség 4-6-szorosát meghaladó vágási sebességgel. gyorsvágók által megengedett.
A kemény ötvözetek hátránya a fokozott törékenység.
Jelenleg a Szovjetunióban két keményötvözet-csoportot gyártanak. A főbbek azok volfrám(VK2, VKZ, VK4, VK6M, VK6, VK8 és VK8M) és titán-volfrám(T30K4, T15K6, T14K8, T5K10). Ezen csoportok mindegyike sajátos alkalmazási területtel rendelkezik (2. táblázat).
Minden volfrámötvözet öntöttvas, színesfémek és ötvözeteik, edzett acélok, rozsdamentes acélok és nemfémes anyagok (keménygumi, porcelán, üveg stb.) feldolgozására szolgál. A titán-volfrám csoportba tartozó keményötvözeteket acélok feldolgozására használják.
Kerámia anyagok. A közelmúltban a szovjet kohászok olcsó, magas forgácsolási tulajdonságokkal rendelkező anyagokat hoztak létre, amelyek sok esetben helyettesítik a keményötvözeteket. Ezek kerámia anyagok ( termokorund), fehér, márványra emlékeztető lemezek formájában készülnek, amelyeket a keményötvözetekhez hasonlóan vagy a vágótartókhoz forrasztanak, vagy mechanikusan rögzítenek hozzájuk. Ezek a lemezek nem tartalmaznak olyan drága és ritka elemeket, mint a volfrám, titán stb. Ugyanakkor a kerámia lemezek a keményötvözeteknél nagyobb keménységgel tűnnek ki, és 1200°-ra hevítve is megtartják keménységüket, ami lehetővé teszi a fémek vágását nagy vágási sebesség.
A kerámia lemezek hátránya az elégtelen viszkozitás. A kerámiabetétes vágószerszámok öntöttvas, bronz, alumíniumötvözetek és lágyacélok megmunkálására vagy félkészítésére használhatók.
6. Vágók élezése és kikészítése
A gyárakban a marók élezését általában központilag, élezőgépeken végzik speciális munkások. De magának az esztergályosnak tudnia kell élezni és megmunkálni a marókat.
2. táblázat
Egyes keményötvözetfajták tulajdonságai és rendeltetése

A nagy sebességű marók élezése és simítása az alábbi szabályok betartásával történik:
1. A csiszolókorong ne üssön, felülete sima legyen; Ha a kör munkafelülete elhasználódott, azt ki kell javítani.
2. Élezéskor szerszámot kell használnia, és nem kell felfüggeszteni a vágót. A szerszámtartót a lehető legközelebb kell felszerelni a csiszolókoronghoz, a kívánt szögben, és megbízhatóan támasztja meg a marót (50. ábra, a-d).
3. Az élezendő vágót a kör munkafelülete mentén kell mozgatni, különben egyenetlenül kopik.
4. Annak érdekében, hogy ne melegítse túl a vágót, és ezáltal elkerülje a repedések megjelenését, ne nyomja túl erősen a vágót a kerékhez.
5. Az élezést a vágó folyamatos és bőséges vízzel történő hűtésével kell végezni. A csepegtető hűtés, valamint a nagyon forró vágógép időszakos vízbe merítése nem megengedett. Ha a folyamatos hűtés nem biztosítható, célszerű száraz élezésre váltani.
6. A gyorsacél marók élezését közepes keménységű, 25-16-os szemcseméretű elektrokorund tárcsákkal kell elvégezni.
A vágóélek élezésének sorrendje a következő. Először élesítse meg a fő hátsó felületet (50. ábra, a). Ezután a segéd hátsó felület (50. ábra, b), majd az elülső felület (50. ábra, c) és végül a csúcs görbületi sugara (50. ábra, d).
7. Szigorúan tilos a vágóélek élezése olyan gépeken, amelyeknél a védőburkolatot eltávolították.
8. Élezéskor feltétlenül viseljen védőszemüveget.
A vágó élezése után apró bevágások, sorja és karcolások maradnak a vágóéleken. Speciális simítógépeken végzett kikészítéssel küszöbölhetők ki. A kikészítés manuálisan is történik ásványolajjal megnedvesített finomszemcsés fenőkő segítségével. Először a fenőkő könnyű mozdulataival a hátsó felületeket, majd az elülső felületet és a csúcs görbületi sugarát állítjuk be.
Keményfém lapkákkal felszerelt marók élezése és simítása. A keményfém lapos marók élezése zöld szilícium-karbid körökkel ellátott élezőgépeken történik. Az élezés mind kézzel (50. ábra, a-d), mind a szerszámtartókban rögzített marókkal történik. Ezeknek a maróknak az élezési eljárása megegyezik a gyorsacél marókéval, azaz először a fő hátlap mentén (50. ábra, a), majd a kiegészítő hátsó felületek mentén (50. ábra, b), és majd az elülső felület mentén (50. ábra, c) és végül a maró csúcsa mentén (50. ábra, d).

Az előélezés 50-40-es szemcsefinomságú zöld szilícium-karbid kerekekkel, a végső élezés 25-16-os szemcsemérettel történik.
A vágót nem szabad túl erősen a kerék munkafelületéhez nyomni, hogy elkerüljük a keményfém lemez túlmelegedését és megrepedését. Ezenkívül folyamatosan mozgatni kell a körhöz képest; ez szükséges a kör egyenletes kopásához.
Az élezés történhet szárazon vagy a vágó bő vízzel történő hűtésével.
A keményfém vágó élezése után a felületét polírozni kell. A kikészítés manuálisan vagy befejezőgépen történik. A kézi simítás öntöttvas vagy rézlappal történik, melynek munkafelületét speciális pasztával dörzsöljük, vagy gépolajjal vagy kerozinnal kevert bór-karbid port egyenletes rétegben hordjuk fel a felületre. A simítást a vágóéltől számított 2-4 mm szélességben végezzük.
A kikészítés hatékonyabb egy speciális befejező gépen, 250-300 mm átmérőjű, 1,5-2 m/sec sebességgel forgó öntöttvas koronggal; gépolajjal vagy kerozinnal kevert bór-karbid pasztát vagy port hordunk fel ennek a korongnak a felületére.
7. Forgácsképződés
A chipek típusai. A leválasztott forgácsok a vágónyomás hatására nagymértékben megváltoztatják az alakjukat, vagy ahogy mondani szokták, deformálódnak: hosszuk lerövidül, vastagsága megnő. Ezt a jelenséget először Prof. I. A. Idő és neve forgácszsugorodás.
A forgácsok megjelenése a fém mechanikai tulajdonságaitól és a vágás körülményeitől függ. Ha viszkózus fémeket dolgozunk fel (ólom, ón, réz, lágyacél, alumínium stb.), akkor a forgácsok egyes elemei egymáshoz szorosan tapadva folyamatos, szalaggá tekeredő forgácsot képeznek (51. ábra, a). Az ilyen forgácsokat hívják csatorna. Kevésbé viszkózus fémek, például keményacél feldolgozásakor az egyes elemekből forgács keletkezik (51. ábra, b), amelyek gyengén kapcsolódnak egymáshoz. Az ilyen forgácsokat hívják forgács aprítása.
Ha a megmunkálandó fém törékeny, például öntöttvas vagy bronz, akkor a forgács egyes elemei eltörnek, és elválik a munkadarabtól és egymástól (51. ábra, c). Az ilyen, szabálytalan alakú egyedi pelyhekből álló forgácsokat nevezik törési forgács.

A figyelembe vett forgácstípusok nem maradnak állandóak, változhatnak a változó vágási körülményekkel. Minél lágyabb a megmunkálandó fém, és minél kisebb a forgácsvastagság és a vágási szög, annál jobban megközelíti a forgács alakja a lefolyót. Ugyanez figyelhető meg a vágási sebesség növelésével és a hűtéssel. A vágási sebesség csökkenésével a forgács leürítése helyett forgács keletkezik.
Növekedés. Ha megvizsgáljuk a vágáshoz használt maró elülső felületét, akkor a vágóélen időnként egy kis fémcsomót találhatunk, amely magas hőmérséklet és nyomás hatására a maróra hegesztett. Ez az ún növekedés(52. ábra). Ez bizonyos körülmények között megjelenik kemény fémek vágásakor, de nem figyelhető meg törékeny fémek vágásakor. A felhalmozódás keménysége 2,5-3-szor nagyobb, mint a feldolgozandó fém keménysége; ennek köszönhetően maga a növekedés képes levágni a fémet, amelyből kialakult.

A beépített él pozitív szerepe, hogy befedi a vágópengét, megvédve azt a lehulló forgácsok és a hőhatások okozta kopástól, és ez némileg növeli a vágó tartósságát. A lerakódások jelenléte hasznos hámozáskor, mivel a vágópenge kevésbé melegszik fel, és csökken a kopása is. A felrakódások kialakulásával azonban a megmunkált felület pontossága és tisztasága romlik, mivel a felrakódás torzítja a penge alakját. Ezért a felhalmozódás kialakulása veszteséges a befejező munkák során.
8. Vágási mód elemeinek fogalma
A feldolgozás minden egyes esetben hatékonyabb elvégzése érdekében az esztergályosnak ismernie kell a vágási mód alapelemeit; ezek az elemek a vágásmélység, az előtolás és a vágási sebesség.
Vágásmélység a megmunkált és megmunkált felületek távolsága, az utóbbira merőlegesen mérve. A fogásmélységet t betű jelöli, és milliméterben mérjük (53. ábra).

A munkadarab esztergagépen történő esztergálásakor a megmunkálási ráhagyás egy vagy több menetben levágásra kerül.
A t vágási mélység meghatározásához meg kell mérni a munkadarab átmérőjét a vágó áthaladása előtt és után, az átmérők közötti különbség fele megadja a vágási mélységet, más szóval,
ahol D az alkatrész átmérője mm-ben, mielőtt a maró áthaladna; d az alkatrész átmérője mm-ben a maró áthaladása után. A maró munkadarabonkénti mozgását (53. ábra) ún iktatás. Az előtolást s betű jelöli, és milliméterben mérik az alkatrész fordulatánként; A rövidség kedvéért szokás írni mm/ford. Attól függően, hogy a vágó milyen irányban mozog a keretvezetőkhöz képest, vannak:
A) hosszanti előtolás- az ágyvezetők mentén;
b) kereszttáplálás- merőleges az ágyvezetőkre;
V) ferde takarmány- szögben az ágyvezetőkkel (például kúpos felület forgatásakor).
Vágás keresztmetszeti területe f (ef) betűvel jelölve, és a fogásmélység és az előtolás szorzataként definiálva (lásd 53. ábra):
A vágási mélység és az előtolás mellett a vágási réteg szélességét és vastagságát is megkülönböztetjük (53. ábra).
Vágási réteg szélessége, vagy forgácsszélesség, - a megmunkált és megmunkált felületek távolsága, a vágási felület mentén mérve. Mérése milliméterben történik, és b (be) betűvel jelöljük.
A vágott réteg vastagsága, vagy forgácsvastagság, - a forgácsolóél két egymást követő helyzete közötti távolság az alkatrész fordulatonként, a forgács szélességére merőlegesen mérve. A forgács vastagságát milliméterben mérik, és a betűvel jelölik.
Ugyanazon előtolásnál és fogásmélységnél, a φ főszög csökkenésével a forgácsvastagság csökken, a szélessége pedig nő. Ez javítja a hőelvonást a vágóélről és növeli a vágó tartósságát, ami viszont lehetővé teszi a vágási sebesség jelentős növelését és nagyobb számú alkatrész feldolgozását egységnyi idő alatt. A φ főszög csökkenése azonban a sugárirányú (taszító) erő növekedéséhez vezet, ami a nem kellően merev részek feldolgozása során azok megereszkedését, pontosságvesztést, valamint erős rezgéseket okozhat. A rezgések megjelenése pedig a megmunkált felület tisztaságának romlásához vezet, és gyakran a maró vágóélének letöredezését okozza.
Vágási sebesség. Esztergagépen történő megmunkáláskor a D átmérőjű körön elhelyezkedő A pont (54. ábra) az alkatrész egy fordulatával ennek a körnek a hosszával megegyező utat halad át.

Bármely kör hossza körülbelül 3,14-szerese az átmérőjének, tehát egyenlő 3,14 D-vel.
A 3,14-es számot, amely azt mutatja, hogy a kör hossza hányszor nagyobb, mint az átmérője, általában a görög π (pi) betűvel jelölik.
Az A pont egy fordulat alatt πD-vel egyenlő távolságot tesz meg. Az alkatrész D átmérőjét, valamint kerületének πD hosszát milliméterben mérjük.
Tegyük fel, hogy a munkadarab percenként több fordulatot is megtesz. Jelöljük számukat n fordulat/perc vagy rövidített fordulatszám betűvel. Az A pont által megtett út egyenlő lesz a kerület és a percenkénti fordulatok számának szorzatával, azaz πDn milliméter per perc vagy rövidítve mm/perc. perifériás sebesség.
A megmunkált felület egy pontja által a maró vágóéléhez képest egy perc alatt elfordulva megtett utat ún. vágási sebesség.
Mivel az alkatrész átmérőjét általában milliméterben adják meg, a vágási sebesség méter/percben történő meghatározásához el kell osztani a πDn szorzatot 1000-rel. Ez a következő képlettel írható fel:
ahol v a vágási sebesség m/percben;
D a munkadarab átmérője mm-ben;
n az alkatrész percenkénti fordulatszáma.
3. példa Megmunkált henger D = 100 = 150 ford./perc átmérővel. Határozza meg a vágási sebességet.
Megoldás: Orsó fordulatszám számlálás. Ismert átmérőjű alkatrész megmunkálásakor előfordulhat, hogy egy esztergálónak ilyen számú orsófordulatra kell beállítania a gépet a kívánt vágási sebesség eléréséhez. Ehhez a következő képletet használják: ahol D a munkadarab átmérője mm-ben;
4. példa Mekkora fordulatszámú percenként kell lennie egy D = 50 mm átmérőjű hengernek v = 25 m/perc forgácsolási sebesség mellett?
Megoldás:
9. Alapvető információk a maróra ható erőkről és a vágóerőről
A vágóra ható erők. A forgácsok munkadarabról történő eltávolításakor a vágónak le kell győznie a fémrészecskék egymáshoz való tapadási erejét. Amikor a maró vágóéle belevág a megmunkálás alatt álló anyagba és a forgácsot leválasztják, a maró nyomást gyakorol a leválasztott fémre (55. ábra).

A P z erő felülről lefelé nyomja le a vágót, ami hajlamos lefelé nyomni a marót és felfelé hajlítani az alkatrészt. Ezt az erőt ún vágóerő.
A vízszintes síkban az előtolás mozgásával ellentétes irányban a P x, ún axiális erő, vagy tápláló erő. Hosszirányú esztergálás során ez az erő a vágószerszámot a farokrész felé tolja.
A vízszintes síkban, az előtolás irányára merőlegesen P y erő nyomja a marót, amit radiális erőnek nevezünk. Ez az erő hajlamos arra, hogy a marót eltolja a munkadarabtól, és vízszintes irányba hajlítsa.
Az összes felsorolt erőt kilogrammban mérik.
A három erő közül a legnagyobb a függőleges forgácsolóerő: körülbelül négyszerese az előtolási erőnek és 2,5-szerese a radiális erőnek. A vágóerő megterheli a támasztószerkezet alkatrészeit; a vágót és az alkatrészt is terheli, gyakran nagy feszültséget okozva bennük.
Kísérletek során bebizonyosodott, hogy a forgácsolóerő függ a megmunkálandó anyag tulajdonságaitól, az eltávolított forgács méretétől és keresztmetszeti alakjától, a maró alakjától, a vágási sebességtől és a hűtéstől.
A különféle anyagok forgácsolási ellenállásának jellemzésére kialakították a vágási együttható fogalmát. A K vágási együttható a vágási nyomás kilogramm/négyzetmilliméterben a vágott szakaszon, bizonyos vágási körülmények között mérve:
Vágási mélység t.............5 mm
Előtolás s...................1 mm/ford
Rajzszög γ................................15°
Vezetési szög φ......45°
A vágóél egyenes, vízszintes
A maró csúcsa r = 1 mm sugárral van lekerekítve
A munka hűtés nélkül történik
táblázatban A 3. táblázat egyes fémek forgácsolási együtthatójának átlagos értékeit mutatja.
3. táblázat
A K forgácsolási együttható átlagértékei esztergálás közben

Ha ismert a K vágási együttható, akkor megszorozva az f vágás keresztmetszeti területével mm 2 -ben, a képlet segítségével megtalálhatja a forgácsolóerő hozzávetőleges értékét
P z = Kf kg. (8)
5. példa. Esztergagépen egy σ b = 60 kg/mm2-es gépi acéltengelyt esztergatunk. Határozza meg a vágási erőt, ha a vágási mélység t = 5 mm és az előtolás s = 0,5 mm/ford.
Megoldás. A (8) képlet szerint a forgácsolóerő P z = Kf kg. (8) Meghatározzuk f értékét: f = ts = 5x0,5 = 2,5 mm 2. táblázat szerint A 3. ábrán megtaláljuk a K értékét σ b = 60 kg/mm 2 gépacél esetén: K = 160 kg/mm 2. Ezért z = Kf = 160x2,5 = 400 kg. Vágási teljesítmény. A vágási erő és vágási sebesség ismeretében megtudhatja, mekkora teljesítmény szükséges egy adott szakasz forgácsának vágásához.
A vágási teljesítményt a képlet határozza meg (9) ahol N pe - vágási teljesítmény LE-ben;
P z - vágóerő kg-ban;
v - vágási sebesség m/percben.
A gép villanymotorjának teljesítménye valamivel nagyobb legyen, mint a vágóteljesítmény, mivel az elektromos motor erejének egy részét a súrlódás leküzdésére fordítják azokban a mechanizmusokban, amelyek az elektromos motorról a gép orsójára továbbítják a mozgást.
6. példa. Határozza meg az előző példában figyelembe vett tengely forgácsolási teljesítményét, ha a feldolgozást υ = 60 m/min forgácsolási sebességgel végezzük. Megoldás . A (9) képlet szerint vágási teljesítmény
A vágási teljesítményt általában kilowattban (kW) fejezik ki lóerő helyett. Egy kilowatt 1,36-szoros lóerő, tehát a teljesítmény kilowattban történő kifejezéséhez el kell osztani a lóerőt 1,36-tal:
és fordítva,
10. Vágási hő és a szerszám élettartama
A vágóerő növekedésével a súrlódási erő növekszik, ami a vágási folyamat során keletkező hőmennyiség növekedését eredményezi. A vágási hő a vágási sebesség növelésével még jobban megnő, mivel ez felgyorsítja a forgácsképződés teljes folyamatát.
Az el nem távolított vágási hő kellően meglágyítja a marót, aminek következtében a vágórészének kopása intenzívebben jelentkezik. Emiatt ki kell cserélni a vágót, vagy meg kell élezni, és vissza kell szerelni.
A maró tompítás előtti folyamatos működésének idejét a vágó tartósságának (percben mérve) nevezzük. A kések gyakori cseréje (alacsony tartósság) többletköltséget okoz a vágó élezésénél és felszerelésénél, valamint az elhasználódott vágószerszámok utánpótlásánál.
Ezért a szerszám élettartama fontos tényező a vágási feltételek megválasztásakor, különösen a vágási sebesség kiválasztásakor.
A vágó tartóssága elsősorban az anyag minőségétől függ, amelyből készült. A legellenállóbb olyan vágó lesz, amely olyan anyagból készül, amely lehetővé teszi a legmagasabb fűtési hőmérsékletet jelentős keménységveszteség nélkül. A legellenállóbbak a keményfém lemezekkel és ásványi-kerámia lemezekkel felszerelt marók; lényegesen kisebb tartósság - gyorsacélból készült marók, legkevésbé - karbon szerszámacélból készült marók.
A vágó tartóssága a megmunkálandó anyag tulajdonságaitól, a vágási szakasztól, a vágó élezési szögeitől és a vágási sebességtől is függ. A megmunkálandó anyag keménységének növekedése csökkenti a vágó tartósságát.
Az élezési szögek és az elülső felület alakjának változtatásával jelentős mértékben növelheti a marók tartósságát és termelékenységét.
A vágási sebesség különösen erősen befolyásolja a szerszám élettartamát. Néha még a legkisebb sebességnövekedés is a vágó gyors eltompulásához vezet. Például, ha az acél nagy sebességű maróval történő megmunkálásakor csak 10%-kal, azaz 1,1-szeresére növeli a vágási sebességet, akkor a vágószerszám kétszer olyan gyorsan eltompul, és fordítva.
A vágás keresztmetszeti területének növekedésével a szerszám élettartama csökken, de nem annyira, mint a vágási sebesség azonos növekedése esetén.
A vágó tartóssága függ a vágó méretétől, a vágott rész alakjától és a hűtéstől is. Minél masszívabb a vágó, annál jobban távolítja el a hőt a vágóélről, és így annál nagyobb a tartóssága.
A kísérletek azt mutatják, hogy ugyanazon vágási szakaszon nagyobb fogásmélység és kisebb előtolás nagyobb szerszámélettartamot biztosít, mint kisebb fogásmélység megfelelően nagyobb előtolással. Ez azzal magyarázható, hogy nagyobb vágásmélység esetén a forgács a vágóél nagyobb hosszával érintkezik, így a vágási hő jobban eloszlik. Éppen ezért ugyanazon vágási szakaszon kifizetődőbb nagyobb mélységgel dolgozni, mint nagyobb előtolással.
A vágó tartóssága jelentősen megnő, ha lehűtjük.
A hűtőfolyadékot bőségesen kell adagolni (emulzió 10-12 l/perc, olaj és szulfofrezol 3-4 l/perc); egy kis mennyiségű folyadék nem hogy nem hoz semmi hasznot, de még rontja is a vágót, aminek következtében apró repedések jelennek meg a felületén, ami csorbuláshoz vezet.
11. Vágási sebesség kiválasztása
A munka termelékenysége a vágási sebesség megválasztásától függ: minél nagyobb vágási sebességgel történik a feldolgozás, annál kevesebb időt fordítanak a feldolgozásra. A vágási sebesség növekedésével azonban a maró tartóssága csökken, így a vágási sebesség megválasztását befolyásolja a maró tartóssága és mindazok a tényezők, amelyektől a maró tartóssága függ. Ezek közül a legfontosabbak a megmunkálandó anyag tulajdonságai, a vágóanyag minősége, a fogásmélység, az előtolás, a vágóméretek és az élezési szögek, valamint a hűtés.
1. Minél hosszabb a szerszám élettartama, annál kisebb vágási sebességet kell választani, és fordítva.
2. Minél keményebb a megmunkálandó anyag, annál kisebb a vágó tartóssága, ezért a kemény anyagok megmunkálásakor szükséges tartósság biztosítása érdekében csökkenteni kell a vágási sebességet. Öntött és kovácsolt munkadarabok feldolgozásakor, amelyeknek felülete kemény kéreggel, héjjal vagy pikkelyes, csökkenteni kell a vágási sebességet a kéreg nélküli anyagok feldolgozásakor lehetségeshez képest.
3. Tartóssága a vágóanyag tulajdonságaitól függ, ezért a vágási sebesség megválasztása is ezektől a tulajdonságoktól függ. Ha minden más tényező azonos, a nagysebességű acélvágók lényegesen nagyobb vágási sebességet tesznek lehetővé, mint a szénacél marók; Még nagyobb vágási sebességet tesznek lehetővé a keményfém ötvözetekkel felszerelt marók.
4. A vágó tartósságának növelése érdekében viszkózus fémek megmunkálásakor előnyös a marók hűtését alkalmazni. Ilyenkor azonos szerszámélettartam mellett 15-25%-kal lehet növelni a forgácsolási sebességet a hűtés nélküli megmunkáláshoz képest.
5. A vágó méretei és élezési szögei is befolyásolják a megengedett vágási sebességet: minél masszívabb a vágó, különösen a feje, annál jobban elvezeti a vágás során keletkező hőt. A rosszul megválasztott vágószögek, amelyek nem felelnek meg a megmunkált anyagnak, növelik a vágóerőt és hozzájárulnak a vágó gyorsabb kopásához.
6. A vágási keresztmetszet növekedésével a maró tartóssága csökken, ezért nagyobb keresztmetszetnél kisebb vágási sebességet kell választani, mint kisebb keresztmetszetnél.
Mivel a simító megmunkálás kis keresztmetszetű forgácsot távolít el, a simító megmunkálás során a forgácsolási sebesség lényegesen nagyobb lehet, mint a nagyoló megmunkálásnál.
Mivel a vágási keresztmetszet növelése kevésbé befolyásolja a szerszám élettartamát, mint a forgácsolási sebesség növelése, a vágási sebesség enyhe csökkentésével célszerű a vágási keresztmetszetet növelni. A Kuibisev Szerszámgépgyár V. Kolesov innovatív esztergályosának feldolgozási módszere ezen az elven alapul. A 150 m/perc forgácsolási sebességgel dolgozó T. Kolesov az acél alkatrészeket 0,3 mm/fordulat helyett 3 mm/fordulatig terjedő előtolással fejezi be, és ez a gépi idő 8-10-szeres csökkenéséhez vezet.
Felmerül a kérdés: miért növelik a fejlett esztergák gyakran a termelékenységet a vágási sebesség növelésével? Ez nem mond ellent a vágás alaptörvényeinek? Nem, ez nem mond ellent. Csak olyan esetekben növelik a vágási sebességet, amikor a vágási keresztmetszet növelésének lehetőségét teljes mértékben kihasználták.
Fél- vagy simító megmunkálásnál, ahol a fogásmélységet kis megmunkálási ráhagyás korlátozza, és az előtolást a nagy megmunkálási tisztaság követelményei korlátozzák, a forgácsolási sebesség növelésével a forgácsolási feltételek növelése lehetséges. Ezt teszik a haladó esztergák, akik fél- és simító megmunkálásban dolgoznak. Ha lehetséges nagy vágási szakaszokkal dolgozni (nagy ráhagyással), akkor mindenekelőtt a lehető legnagyobb vágási mélységet, majd a legnagyobb technológiailag megengedett előtolást és végül a megfelelő vágási sebességet kell kiválasztani.
Azokban az esetekben, amikor a megmunkálási ráhagyás kicsi, és a felület tisztaságára nincs különösebb követelmény, a forgácsolási módot a lehető legnagyobb előtolás alkalmazásával kell növelni.
12. A kezelt felület tisztasága
Vágóval történő megmunkáláskor az alkatrész megmunkált felületén mindig maradnak egyenetlenségek mélyedések és bordák formájában, még a leggondosabb megmunkálás esetén is. Az egyenetlenségek magassága a feldolgozási módtól függ.
A gyakorlat azt állapította meg, hogy minél tisztább az alkatrész felülete, annál kevésbé van kitéve a kopásnak és korróziónak, és annál erősebb az alkatrész.
A gondos felületkezelés egy alkatrész megmunkálásakor mindig drágább, mint a durva felületkezelés. Ezért a kezelt felület tisztaságát az alkatrész üzemi körülményeitől függően kell meghatározni.
A felület tisztaságának feltüntetése rajzokon. A GOST 2789-59 szerint a felületi tisztaságnak 14 osztálya van. Az összes tisztasági osztály megjelölésére egy táblát kell felszerelni - egy egyenlő oldalú háromszöget, amely mellett az osztályszám szerepel (például 7; 8; 14). A legtisztább felületek a 14. osztályba, a legdurvábbak pedig az 1. osztályba tartoznak.
A felület érdességét a GOST 2789-59 szerint két paraméter egyike határozza meg: a) az R a profil számtani átlagos eltérése és b) az R z egyenetlenségek magassága.
Az érdesség mérésére és a kezelt felület egy adott osztályhoz való hozzárendelésére speciális mérőműszereket használnak, amelyek a felületi profil vékony gyémánttűvel történő tapintásának módszerén alapulnak. Az ilyen eszközöket profilométereknek és profilográfoknak nevezik.
Az érdesség meghatározásához és a kezelt felület egy vagy másik tisztasági osztályba való besorolásához műhelyi körülmények között különböző tisztasági osztályok tesztelt mintáit használják - az úgynevezett tisztasági szabványokat, amelyekkel összehasonlítják az alkatrész feldolgozott felületét.
A megmunkált felület tisztaságát befolyásoló tényezők. A gyakorlat bebizonyította, hogy a megmunkált felület tisztasága számos októl függ: a megmunkálandó anyagtól, a maró anyagától, az élezési szögektől és a vágóélek állapotától, az előtolástól és a vágási sebességtől, a kenési és hűtési tulajdonságoktól. a folyadék, a gép-vágó-munkadarab rendszer merevsége stb.
A jó minőségű felület eléréséhez esztergáláskor különösen fontos a vágási sebesség, az előtolás, a bemeneti szögek és a vágócsúcs görbületi sugara. Minél kisebb az előtolás és a bevezető szög, és minél nagyobb a csúcs görbületi sugara, annál tisztább a megmunkált felület. A vágási sebesség nagymértékben befolyásolja a felület minőségét. Acél 100 m/perc-nél nagyobb forgácsolási sebességgel történő esztergálásakor a megmunkált felület tisztább, mint 25-30 m/perc sebességnél.
A tisztább megmunkált felület elérése érdekében ügyeljen a vágóélek gondos élezésére és megmunkálására.
Ellenőrző kérdések 1. Milyen alakú forgács keletkezik képlékeny fémek feldolgozása során? Törékeny fémek feldolgozásakor?
2. Nevezze meg a vágófej fő elemeit!
3. Mutassa be a metszőfog elülső és hátsó felületét; elülső és hátsó szögek; pontszög.
4. Mi a célja a vágó első és hátsó sarkának?
5. Mutassa be a fő vágóél vezetési szögeit és dőlésszögét.
6. Milyen anyagokból készülnek a vágók?
7. Milyen minőségű keményötvözeteket használnak az acélfeldolgozásban? Öntöttvas feldolgozásakor?
8. Sorolja fel a vágási mód elemeit!
9. Milyen erők hatnak a vágóra?
10. Milyen tényezők és hogyan befolyásolják a forgácsolóerő nagyságát?
11. Mi határozza meg a vágó tartósságát?
12. Milyen tényezők befolyásolják a vágási sebesség megválasztását?
A vágó szögei a vágórész fő geometriai paramétereire vonatkoznak. Meghatározásuk, helyzetük és nagyságuk attól függően változik, hogy a forgácsolási folyamat során, vagy a megmunkálás alatt álló munkadarabbal nem kapcsolódnak-e, azaz geometriai testhez hasonlóan.
Tekintsük a maró szögeit egy geometriai test szögeinek (1. ábra). A könnyebb érthetőség érdekében meg kell adni a vágószögek definícióit.
Fő- és segédvágó szögek
Alatt fő sík a hosszanti és keresztirányú előtolás irányával párhuzamos síkra utal.
ábra - Fő- és segédszögek felülnézetben
φ a fő vágóél fősíkra való vetülete és a hosszirányú előtolás iránya között helyezkedik el.
Segédszög φ1 a segédvágóél fősíkra való vetülete és a hosszirányú előtolás iránya között helyezkedik el.
Csúcsszög(a tervben) e a fő- és a segédél fősíkra való vetületei között helyezkedik el.
A fő vágóél dőlésszöge λ, a fő vágóél és a maró csúcsán keresztül a fősíkkal párhuzamos vonal között helyezkedik el. Mérése a fő vágóélen átmenő síkon is a fősíkra merőlegesen történik. Sarok Nak nek pozitívnak tekintendő, ha a vágóél a fő vágóél legalacsonyabb pontja, és negatív, ha a vágóél csúcsa a fő vágóél legmagasabb pontja, és golyó által sebzett, ha a fő vágóél párhuzamos a fő vágóéllel.
A φ és φ1 és ε szögeket is a fősíkon mérjük.
Első és hátsó szögek
A maró elülső és hátsó szögének meghatározásához be kell vezetni a fő vágási sík fogalmát, amelyben mérni kell
ezeket a szögeket. Célszerű a fősíkra és a fő vágóél e síkra való vetületére merőleges NN síkot venni.
Egy ilyen vágási sík kis mértékben tér el attól a síktól, amelyben a forgácsleválasztás folyamata a vágás során megtörténik, ráadásul leegyszerűsíti a vágószögek mérését.
Fő hátsó sarok α a hátsó felületet érintő sík és a fő vágóélen átmenő, a fősíkra merőleges sík között helyezkedik el.
Fő dőlésszög γ a gereblye felületét érintő sík és a fő vágóélen átmenő, a fősíkkal párhuzamos sík között helyezkedik el.
Meg kell különböztetni a kiegészítő hátsó szöget is α 1, a fősíkra és a segédvágóél e síkra való vetületére merőleges vágósíkban mérve. A hátsó felületet érintő sík és a fősíkra merőleges segédvágóélen átmenő sík között helyezkedik el.
A maró fő szögeit, a gereblyét és a háttámla általában az NN fő vágási síkban kell megadni. A gyártás során azonban más vágósíkban elhelyezkedő szögekkel kell dolgozni. Például a hosszanti síkban /-/ (ápr., ex), a maró tengelyével párhuzamosan és a fősíkra merőlegesen, valamint a keresztirányú síkban helyezkedik el //-// (apop, upop) a maró és a fősík tengelyére merőlegesen helyezkedik el.
A szögek közötti függőség
Határozzuk meg az összefüggéseket ezen szögek között.
Rizs. 1 Vágószögek meghatározása különböző síkokban
ábrán. Az 1. ábra a következő síkokat mutatja:
DEFG- a hossz- és keresztirányú előtolás irányával párhuzamos fősík (ebben az esetben egybeesik a maró referenciasíkjával és a rajz síkjával);
ABGF- a vágóélen áthaladó sík AB merőleges a fősíkra;
ABGF- egy sík, amely a hátsó síkot ábrázolja a hátsó sarkok, és az elülső síkot az elülső sarkok figyelembevételekor;
MNF- síkkal párhuzamos sík ABDEés szöget zár be λ;
BAN BENDGÉs AE.F.- a vágótestet korlátozó síkok, merőlegesek a fősíkra és a vágóél e síkra való vetületére.
Bármely ponton átmegyünk R vágóél három kívánt sík:
ROK, amelyben az a és y szögek találhatók;
ROG ahol a sarkok találhatók áprilisÉs y pr;
ROF,és melyek a sarkok egy popÉs y pop;
Vonal GF sík kereszteződések ABGF a fősíkkal ω szöget zár be a vágóél vetületével.
A vágófejnek a következő elemei vannak: gereblye felület, oldalfelületek, vágóélek és csúcs.
A gereblye felület a vágó azon felülete, amelyen a forgács folyik.
A hátsó felületek a marónak a munkadarab felé néző felületei (fő- és segédanyag).
A vágóéleket az elülső és a hátsó felület metszéspontja képezi; kettő van belőlük - a fő vágóél és a segédél.
A fő vágóél végzi a fő vágási munkát. Az elülső és a fő hátsó felületek metszéspontjából alakul ki.
A segédvágóél (az elülső és a hátsó segédfelület metszéspontjából) van kialakítva.
A vágó hegye a fő és a segédvágóél találkozási pontja.
A szögeket a fősíkhoz és a vágási síkhoz viszonyítva kell mérni.
A fősík a hosszanti és keresztirányú előtolás irányával párhuzamos sík. Prizmás testű esztergáló maróknál ennek a síknak a maró alsó tartófelülete vehető.
A vágósík a főre merőleges sík, amely áthalad a maró vágóélén, és érinti a vágási felületet.
Rizs. 15. Vágási folyamat diagramja:
a - vágás kezdete, b - forgácsképződés kezdete, c - vágási folyamat, t - vágásmélység
ábrán. A 15. b ábra a sarkok és egyes felületek jelöléseit mutatja. A szerszám hegyes alakját az 1 elülső felület, amelyen a forgács elcsúszik, és a 2 hátsó felület alkotja. A köztük lévő szöget β pontszögnek nevezzük. A szerszám 2 hátsó felülete és a 3 vágófelület közötti súrlódás csökkentése érdekében ezek a felületek egymáshoz képest általában valamilyen α szögben helyezkednek el, amelyet hátsó szögnek neveznek. Ezt a szöget általában 0 és 16° közötti tartományban veszik, de egyes szerszámoknál (tárcsás és hornyos maróknál) 30°-ig is beállítható.
A maró elülső felülete és a vágási sík közötti, esetünkben a vágási felülettel egybeeső szöget δ vágási szögnek nevezzük (lásd 15. ábra). A szerszám gereblye felülete és a forgácsolási síkra merőleges, a fő vágóélen átmenő sík által alkotott szöget γ szögnek nevezzük. Lágy anyagok megmunkálásakor ez a szög 20°-nál nagyobb lehet, keményacélok megmunkálásánál 10-15°, kemény öntöttvas megmunkálásánál 5°. Nullára vagy akár negatívra is készül (erős keményfémek feldolgozásakor), ami növeli a δ vágási szöget. A vágási szög növelése növeli a szerszám szilárdságát, és acél keményfém szerszámokkal történő megmunkálásakor használatos, amikor a vágási körülmények különösen intenzívek.
Rizs. 17. :
1 — megmunkált felület, 2 — vágófelület, 3 — megmunkált felület; v— a munkadarab mozgási iránya (a vágási sebesség iránya), s 1 — keresztirányú előtolás, s — hosszirányú előtolás
ábrán. A 17. ábrán egy gyaluvágó látható működés közben. A v nyíl mutatja a megmunkálandó munkadarab mozgási irányát a maróhoz képest. Ez az irány egybeesik a vágási sebesség irányával. Magát a mozgást főnek nevezik. Az s nyíl jelzi az adagolás irányát. Az előtolás iránya párhuzamos a munkadarabon kialakított felülettel.
Hagyományosan ezt az előtolást hosszirányúnak nevezzük, a vágóeszköz merőleges mozgását pedig a nyíl mentén s 1 Nevezzük keresztirányú betáplálásnak.
Az s 1 irányba való elmozdulással a maró egy bizonyos t vágási mélységre áll be, az s irányba haladva pedig az eltávolított S fémréteg kívánt vastagsága érhető el.
Kezelt felület 1 – kezelendő felület; 2. vágófelület - az a felület, amelyet közvetlenül a vágóél vágóéle képez (ebben az esetben egybeesik a vágási síkkal); 3. megmunkált felület – a forgácseltávolítás után a munkadarabon kialakult felület. Tekintsük az ábrán látható vágót. 18. Az s nyíl jelzi a maró hosszirányú (tengelyirányú) előtolási irányát. A 4 fő vágóél fősíkra való vetülete és az előtolás iránya közötti szöget φ fősíkszögnek nevezzük. Ez a szög általában 45 és 90° között van kiválasztva.
Rizs. 18. :
1 - megmunkált felület, 2 - segédvágóél, 3 - vágóél, 4 - fő vágóél; φ - fő síkszög, φ 1 - segédsíkszög, ε - csúcsszög a síkban, γ - fő gereblyeszög, γ 1 - segédhajlásszög, β - fő kúpszög, β 1 - segédkúpszög, α - fődomborzat szög, α 1 — segéddomborzati szög, s — hosszirányú előtolás iránya
A 2 segédvágóél fősíkra való vetülete és az előtolás iránya közötti szöget φ 1 segédsíkszögnek nevezzük. Ez a szög nagysága megegyezik a fő síkszöggel, maróknál legfeljebb 2-3 °.
A fő- és a segédél fősíkra vetületei közötti szöget az ε-síkon csúcsszögnek nevezzük.
Az A-A forgácsolási síkban, amelyet fővágósíknak is neveznek, a fő vágóélhez viszonyított főszögeket mérjük: elöl γ, β pontok és hátul α. A B-B vágósíkban, amelyet segédvágósíknak is neveznek, a segédvágóélhez viszonyítva segédszögeket mérünk: elöl γ 1, pontok β 1 és hátul α 1.
A kezelt felület 1 fésűkagyló megjelenésű. Ilyen felületet kapunk annak eredményeként, hogy a következő munkalöket előtt a maró az előtolás mértékével mozog (gyaluláskor). A fésűkagyló egyik oldalát a fő vágóél, a másikat a segédél alkotja.
Minél nagyobbak a bordák, annál nagyobb a kezelt felület érdessége. Az érdesség csökkenthető az előtolás csökkenése, valamint a φ 1 segédszög csökkenése miatt. A befejező munkákra szánt marógépekben a φ 1 szöget néha nullával egyenlővé teszik. Az ilyen marókat pontosan kell elhelyezni a megmunkálandó munkadarabhoz képest.
A szerszám rendeltetésétől és alakjától függően a rajta lévő vágóélek különböző pozíciókat foglalhatnak el, de a fő elemek neve és meghatározása megegyezik.
Bármi is legyen a forgács típusa, kialakulása a vágási zónában lévő anyag deformációjához és tönkremeneteléhez kapcsolódik. A forgácsképzésre fordított energia hővé alakul. A hő nagy részét a forgácsok elszállítják, mivel jelentős deformáción mennek keresztül. Intenzív fémvágáskor a forgács néha vörösen felforrósodik. Egyes anyagokból, például magnéziumötvözetekből származó forgácsok meggyulladhatnak a vágási folyamat során.
A vágási folyamat során felmelegszik a vágóél és a szerszám gereblye felülete is, amelyen a forgács csúszik.
A forgácsok állandó súrlódása az elülső felületen (a szerszámon) felmelegíti a szerszámot, és hozzájárul annak eltompulásához A vágószerszám hőjének nagy részét rá tudják adni, így a szerszám a súrlódástól felmelegedve és a forgácsoktól további hőt kapva túlmelegedhet és elveszítheti vágási tulajdonságait.
A hő és a szerszámkopás csökkentése érdekében vágófolyadékokat (hűtőfolyadékokat) használnak. A feldolgozott anyagtól függően kenő- és hőleadó tulajdonságaikban különbözhetnek egymástól.
A vágási folyamat eredményessége érdekében szükséges, hogy a szerszám munkarésze mindig éles legyen, vágóéle ne sérüljön, a szerszám vágóélét képező felületek tisztán legyenek megmunkálva és ne akadályozzák a forgácseltávolítást.
Egy jól elkészített műszeren ezeket a felületeket tükörfényesre kell hozni.
A vágószerszámok képviselőjének egy esztergavágót választottak, mivel ez a legegyszerűbb.
Az esztergavágó geometriai paramétereinek definíciói más típusú forgácsolószerszámokra is érvényesek, figyelembe véve azok kinematikus marómintázatának sajátosságait.
Az esztergavágó egy munkarészből és egy tartóból áll (1.2. ábra).
Működő rész vágópengéket tartalmaz, és a vágó élezése (újraköszörülése) során keletkezik.
Tartó a vágó rögzítésére szolgál a gép szerszámtartójában.
Elülső felület- a felület, amelyen a forgács folyik.
Fő hátsó felület a munkadarab felületével szemben.
Kiegészítő hátsó felület a munkadarab megmunkált felülete felé nézzen.
Fő vágóél az elülső és a fő hátsó felület metszéspontja alkotja.
Másodlagos vágóél az elülső és a kiegészítő hátsó felületek metszéspontja alkotja.
Rizs. 1.2. Forgató vágó:
1 - elülső felület; 2 - fő hátsó felület; 3 - kiegészítő hátsó felület; 4 - fő vágóél; 5 - kiegészítő vágóél; 6 - a vágó hegye
Vágóvég a fő és a segédél párja egy sugár vagy letörés mentén.
A GOST 25762-83 szerint vannak statikusÉs kinematikai esztergáló szerszámszögek.
Statikus A szögeket egy szerszám rajzának kidolgozásakor, élezésekor és vezérlésekor használják.
Kinematikai A vágószögek a vágási folyamat során alakulnak ki, és a vágási mód paramétereitől (főleg az előtolástól) függenek.
Az esztergaszerszám statikus szögeinek mérése statikus koordinátarendszerben, a kinematikai szögek mérése pedig kinematikai koordinátarendszerben történik. Mind a statikus, mind a kinematikus koordinátarendszer összefügg a maró kinematikájával.
Statikus koordinátarendszer- ez egy téglalap alakú koordináta-rendszer, amelynek origója a forgácsolóél figyelembe vett pontjában van, és a sebesség irányához képest orientált V főmozgás (1.3a ábra). A középtengely mentén szerelt maró esetén a tengely z függőlegesen felfelé irányítva, tengely xÉs y vízszintes síkban helyezkedik el (1.3a. ábra); tengely y a vágótartó tengelye mentén irányítva, tengely x- a maró előtolási iránya mentén.
Esztergaszerszám statikus szögeinek (élezési szögek) mérésére a következő statikus koordinátasíkokat használjuk: fősík, vágósík és munkasík (1.3a ábra).
Fő sík- a vizsgált vágóél vektorra merőleges pontján áthúzott sík V a fő mozgás sebessége (sík OXY).
Vágó sík- a szóban forgó pontban a vágóélt érintő és a fősíkra merőleges sík.
Működő sík- a vektorokon áthaladó sík V fő mozgási sebesség és V s előtolási sebesség (sík OXZ).
Rizs. 1.3. Statikus (a) és kinematikai (b) koordinátarendszerek ( η - vágási sebesség szög)
Az 1.4. ábra egy esztergaszerszám statikus szögeit mutatja.
Fő vágási sík- a fő vágóél fősíkra való vetületére merőleges sík.
Segédvágó sík- a segédvágóél fősíkra való vetületére merőleges sík.
A fő vágási síkban vannak:
fő elülső sarok γ - az elülső felület és a fősík közötti szög. Az elülső felület fősíkhoz viszonyított helyzetétől függően pozitív vagy negatív frontszöget különböztetünk meg (1.4. ábra). Ha az elülső felület egybeesik a fősíkkal, akkor az elülső szög nulla. Az 1.4. ábra egy pozitív dőlésszöget mutat;
fő hátsó sarok α - szög a fő oldalfelület és a vágási sík között;
élezési szög β - a vágógép fő hátsó és elülső felülete közötti szög.
Az 1.4. ábrából az következik:
γ + β + α = 90 0 (1,1)
A szögeket általában beállítják γ És α , és a szög β az (1.1) képlet alapján számítjuk ki.
Mérjen a segédvágási síkban kiegészítő hézagszög α 1 a másodlagos oldalfelület és a fősíkra merőleges másodlagos vágóélen átmenő sík közötti szög.
A fősíkban a síkszögeket mérik:
fő tervszög φ - a fő vágóél fősíkra való vetülete és a munkasík közötti szög;
segédszög a tervben φ 1- a segédvágóél fősíkra való vetülete és a munkasík közötti szög;
csúcsszög a tervben ε - y ol a fő- és a segédvágóél fősíkra való vetületei között.
Rizs. 1.4. Statikus esztergaszerszám szögei:
N-N - fő vágási sík; N 1 -N 1 - segédvágósík
Az 1.4. ábrából az következik:
φ + φ 1 + ε = 180º. (1.2)
Általában szögeket rendelnek hozzá φ És φ 1, és az ε szöget az (1.2) képlet határozza meg.
Fő vágóélszög λ - a vágási síkban elhelyezkedő szög a fő vágóél és a fősík között. Sarok λ lehet pozitív, nulla vagy negatív. Sarok λ egyenlő nullával, ha a fő vágóél a fősíkban van. Az 1.5b ábra a fő vágóél negatív dőlésszögét mutatja.
Rizs. 1.5. Az esztergavágó fő vágóélének λ dőlésszöge [ 3]: a)λ>0, b)λ<0, в)λ = 0
Kinematikai szögek esztergavágó a forgácsolási folyamat során jön létre, és a vágási mód paramétereitől függ (főleg az előtolás értékétől).
Kinematikai koordinátarendszer- ez egy téglalap alakú koordinátarendszer, amelynek origója a forgácsolóél figyelembe vett pontjában van, a sebességhez viszonyítva V e a keletkező vágómozgást (1.3b. ábra).
Az 1.3b ábrából az következik, hogy a kinematikai koordinátarendszer a statikushoz képest egy szöggel el van forgatva η (vágási sebesség szög). Ezenkívül a forgatást a tengelyhez képest hajtják végre y(felszínen OXZ).
Így az esztergaszerszám kinematikai és statikus szögei csak a referencia koordinátasíkjainak helyzetében térnek el egymástól. A szögek meghatározása megegyezik; csak a „statikus” szó helyett a „kinematikus” szót használjuk.
Az alábbiakban néhány legfontosabb meghatározást olvashat.
Kinematikai fősík- a sebességvektorra merőleges sík V e a keletkező vágási mozgást.
Kinematikus vágósík- a fő vágóélt érintő és a kinematikai fősíkra merőleges sík.
Kinematikai merőleges szög γ to - az elülső felület és a kinematikai fősík közötti szög a kinematikai fővágási síkban.
Kinematikus hátsó dőlésszög α to - a kinematikai fővágósíkban a fő hátsó felület és a kinematikai vágási sík közötti szög.
A forgácsolási folyamat során a kinematikus dőlésszög növekszik, és a kinematikus hézagszög csökken a statikus szögekhez képest ( γ to< γ; α k < α ). A többi kinematikai szög (a sík szögei, a fő vágóél dőlésszöge) kissé megváltozik. A vágási szögek ezen változásait általában nem veszik figyelembe. A kinematikai szögek legnagyobb változása a perzisztens marónál következik be. Igen mikor Y= 90º, λ = 0º
γ k = γ + η 1,α k = α - η 1(1.3)
Ahol η - a vágási sebesség szögével megegyező kinematikai komponens:
η = arctan = arctan, (1.4)
ahol Vs az előtolási sebesség, S o a fordulatonkénti előtolás, D a vizsgált vágóél pont átmérője. Nál nél V? V s a kinematikai komponens nullának tekinthető. Ebben az esetben
γ a γ,α-tól α-ig.(1.5)
Az előtolásnál figyelembe kell venni a kinematikai szögek változásait a statikusokhoz képest V sösszemérhető a fő mozgás sebességével V. A kinematikus hátsó szög megváltoztatása különösen veszélyes, mert lehet nulla vagy akár negatív is, ami elfogadhatatlan. Így például nagy menetemelkedésű menetek vágásakor vagy kis átmérőjű lyukak fúrásakor a hézagsarkot a kinematikai komponens figyelembevételével élesíteni kell.
Élezési szögek átmenő marókhoz a statikus vágószögeket élezési szögeknek is nevezik, mert az élezőgép három forgósatu szárán minden szög beállítható. A marók élezési szögei a technológiai rendszer tulajdonságaitól, elsősorban a merevségtől és a rezgésállóságtól függenek. Tehát a dőlésszög átlagos értéke γ egyenlő 10º. Ha azonban a vágóél nincs kivágva, ez a szög 15-20°-ra növelhető. A vágóél keményítéséhez keményítő letörést kell élezni f, szélessége megközelítőleg megegyezik a vágott réteg vastagságával A, szögben γf= 0 - -5º. Az elülső felületen gyakran élesítenek lyukat, hogy biztosítsák a forgácsok felkunkorodását. Hátsó szög α 8-12 fokon belül van.
A nagyolásnál kisebb értékeket, a simításnál a nagyobb értékeket használjuk. Fő tervszög φ 30-90 fok között változik. Alacsonyabb értékeket használnak a technológiai rendszer fokozott merevsége esetén. Sarok φ = Nem merev munkadarabok megmunkálásához 90º-os szög javasolt. Ez a radiális vágóerő csökkenéséhez vezet Pyés a feldolgozási pontosság növelése érdekében. Kiegészítő megközelítési szög φ 1 befolyásolja a megmunkált felület minőségét.
Magas felületminőségi követelmények mellett ezt a szöget 5-10º-ra csökkentik, és néha nullává teszik (tisztító vágóélekkel rendelkező maróknál). Vágóélszög λ befolyásolja a forgácsáramlás irányát és a vágóék szilárdságát. Sarok λ ±5°-on belül változik. Pozitív szögekben λ a forgács a megmunkált felület felé áramlik. Negatívra λ - a kezelendő felület felé.
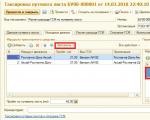